Inspection, Containment, and Rework Services - On-site or at a Vayan Technical Center of Excellence facility.
The increasing complexity of product and supply chains is making quality management even more complex. Vayan is fully committed to preventing nonconforming parts and assemblies from external suppliers or internal manufacturing processes to reach end-users by offering layers of protection to ensure that quality issues are prevented before they cause a broader impact or are resolved quickly after they happen.
Our extensive geographic footprint allows us to quickly deploy well trained teams of full-time personnel with our leading technology in hands to provide the highest-level quality experience and support to OEMs and Tiered Suppliers anytime anywhere.
VAYAN SAFE LAUNCH™
END-OF-LINE INSPECTION
FIREWALLS - CSL1, CSL2, GP-12
INCOMING INSPECTION
PRE-SHIPMENT INSPECTION
MATERIAL COORDINATION
BREAKPOINT MANAGEMENT
PART TRIAL RUN MANAGEMENT
Inspection Part Traceability
We leverage our disciplined process playbook for process and product inspection requirements, part traceability, and rework-quality confirmation. Vayan technology collects inspection data as the work is being performed and share it in real-time through various methods, including among others:
- Product part number, quantity inspected/rejected and pallet/part serial information
- Non-conforming pictures of each reject
- Paretos and trends for problem-solving and breakpoint management
- Time worked for each employee (name, start/end times, etc.)
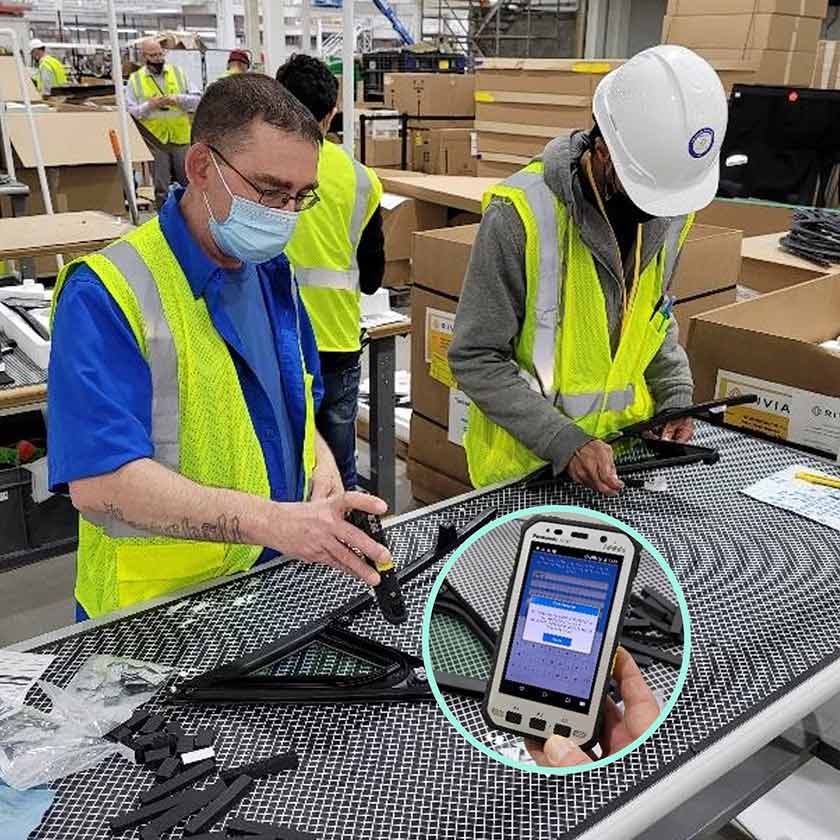
Real-Time Insights and Transparency
Vayan Safe Launch™
Vayan offers a benchmark “Safe Launch™ Playbook”, which is a proactive approach that combines people, process, governance, technology and data excellence to support Tier 1s and/or OEMs to ensure flawless new product launches.
Any potential issues are identified and corrected at the supplier’s or OEM location – from validating supplier processes and controls to inspecting incoming parts, shipping, and labeling – to ensure compliance with quality and safety requirements. In addition to creating a quality wall, Vayan will deploy a layered audit process to ensure process compliance and the desired outcomes of the inspections. Vayan will also allocate full-time or fractional resources to assist with the root cause analysis and corrective action efforts when engineering support is required.
During the safe launch, the Vayan team is an extension of the OEM’s and suppliers’ quality teams, bringing the expertise, resources, and technology to help optimize the quality of new product introductions.
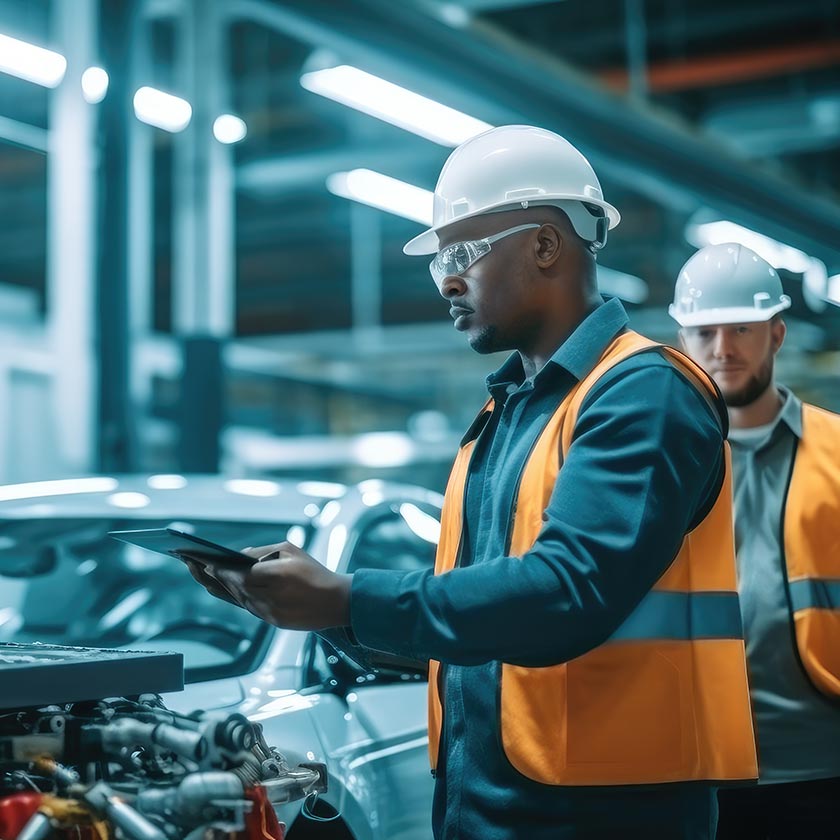